Plenary Talks
Plenary Talk 1
August 1 (Tuesday), 08:30-09:15
Smart Control System for Energy-intensive Equipment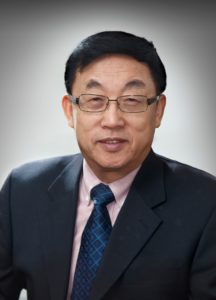
Tianyou Chai
Chair Professor
Center of Automation
Northeastern University, China
China has abundance of mineral resources such as magnesite, hematite and bauxite, which constitute a key component of its economy. The relatively low grade, and the widely varying and complex compositions of the raw extracts, however, pose difficult processing challenges including specialized equipment with excessive energy demands. The energy intensive furnaces together with widely uncertain features of the extracts form hybrid complexities of the system, where the existing modeling, optimization and control methods have met only limited success. Currently, the mineral processing plants generally employ manual control and are known to impose greater demands on the energy, while yielding unreasonable waste and poor operational efficiency. The recently developed Cyber-Physical System (CPS) provides a new key for us to address these challenges. The idea is to make the control system of energy intensive equipment into a CPS, which will lead to a smart control system.
This talk presents the syntheses and implementation of a smart control system for energy-intensive equipment under the framework of CPS. The proposed smart control system consists of three main functions: (i) setpoint control; (ii) tracking control; and (iii) self-optimized tuning. The key in realizing the above functions is the integrated optimal operational control methods to implement setpoint control, tracking control and self-optimized tuning together seamlessly. This talk introduces the integrated optimal operational control methods we proposed.
Hardware and software platform of smart control system for energy-intensive equipment is then briefly introduced, which adopts embedded control system, wireless network and industrial cloud. It not only realizes the functions of computer control system using DCS (PLS), optimization computer and computer for abnormal condition identification and self-optimized tuning, but also achieves the functions of mobile and remote monitoring for industrial process.
Then, using fused magnesium furnace as an example, a hybrid simulation system for smart control system for energy-intensive equipment developed by our team is introduced. The results of simulation experiments show the effectiveness of the proposed method that integrates the setpoint control, tracking control and self-optimized tuning in the framework of CPS.
The industrial application of the proposed smart control system is also discussed. It has been successfully applied to the largest magnesia production enterprise in China, resulting in great returns. Finally, future research on the smart control system is outlined.
Biography: Tianyou Chai received the Ph.D. degree in control theory and engineering in 1985 from Northeastern University, Shenyang, China, where he became a Professor in 1988. He is the founder and Director of the Center of Automation, which became a National Engineering and Technology Research Center and a State Key Laboratory. He is a member of Chinese Academy of Engineering, IFAC Fellow and IEEE Fellow, director of Department of Information Science of National Natural Science Foundation of China.
His current research interests include modeling, control, optimization and integrated automation of complex industrial processes.
He has published 180 peer reviewed international journal papers. His paper titled Hybrid intelligent control for optimal operation of shaft furnace roasting process was selected as one of three best papers for the Control Engineering Practice Paper Prize for 2011-2013. He has developed control technologies with applications to various industrial processes. For his contributions, he has won 4 prestigious awards of National Science and Technology Progress and National Technological Innovation, the 2007 Industry Award for Excellence in Transitional Control Research from IEEE Multiple-conference on Systems and Control.
Plenary Talk 2
August 1 (Tuesday), 09:15-10:00
Digitalization in Utilities and Industries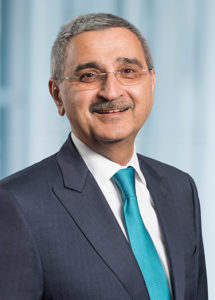
Bazmi Husain
Chief Technology Officer, ABB Group
The world is on the cusp of a fourth industrial revolution driven by a need to enhance productivity. At the same time, increased usage of fossil fuels and the resultant concerns of climate change is driving the shift towards a smarter, greener electrical grid. Both these significant shifts are accelerated by Digitalization. Among the key enablers for Digitalization are the increased availability of data, ubiquitous connectivity between and among machines and people, and the exponential growth in processing power and cheaper storage. Thanks to these developments, machines can be fitted with low-cost sensors, which track and monitor their performance, health and behavior through every stage of their life cycle.
ABB, as the pioneering technology leader, has led the electrical grid since its inception and is a leader in Industrial Automation. ABB has launched Ability, which includes domain specific applications and a platform, built on standards, to enable Utilities and Industries to digitalize their operations. In this talk, we will discuss the challenges and how these are being met. Over 180 Ability applications are available today.
Biography: Bazmi Husain is the Chief Technology Officer of ABB Group.
ABB Group is a pioneering technology leader that helps its customers produce and use electrical power efficiently, to increase industrial productivity and to lower environmental impact in a sustainable way. ABB Group recorded revenue of US$ 34 billion in 2016 and has 135,000 employees.
Bazmi has spent over 35 years at ABB, having worked in different roles including R&D, sales, service, strategy and business operations across different ABB locations, worldwide.
Bazmi is an electrical and electronics engineer and an MS in Physics.
Plenary Talk 3
August 2 (Wednesday), 08:30-09:15
Theory and Technology of Tri-Co Robots
Han Ding
Professor
School of Mechanical Science and Engineering
Huazhong University of Science & Technology, China
The Tri-Co Robots (Coexisting-Cooperative-Cognitive Robots) are those that can naturally interact and collaborate with the operating environment, human as well as other robots, and be adaptive to the complex dynamic environments. The characteristics of Tri-Co robots include: compliant and dexterous structure, multi-modal perception, distributed autonomous and collaborative ability. This talk will introduce the current research activities of robotics in China, especially the Tri-Robot Research Plan of NSFC (National Natural Science Foundation of China), including the scientific challenges, key scientific problems and main research contents of the plan from the aspects of structure, perception and control, followed by the forecasts on China’s expected breakthroughs and goals in Tri-Co robot research domain. After that, the challenges of robotic techniques in machining are analyzed and summarized, and the recent research works in our group are also introduced.
Biography: Prof. Han Ding received his Ph.D. degree in Mechatronics from Huazhong University of Science & Technology in 1989. Supported by the Alexander von Humboldt Foundation, Prof. Ding worked at University of Stuttgart, Germany in 1993. He obtained the National Distinguished Youth Scientific Fund in 1997 and was employed as the “Cheung Kong” Chair Professor at Shanghai Jiao Tong University in 2001. He was elected a member of Chinese Academy of Sciences in 2013.
Prof. Ding has long dedicated himself to the research work in the field of robotics and digital manufacturing and successfully combines the robotics and manufacturing technologies. He published three academic books and more than 300 journal papers, and licensed more than 60 patents in China. Prof. Ding acted as an Associate Editor (2003-2007) and an Editor (2011-) of IEEE Transactions on Automation Science and Engineering. He was a Technical Editor of IEEE/ASME Trans. on Mechatronics from 2010 to 2014. Currently, he is a Senior Editor of IEEE Robotics and Automation Letters. As a General Co-Chair, he hosted the IEEE International Conference on Robotics and Automation held in Shanghai, China in 2011.
Plenary Talk 4
August 2 (Wednesday), 09:15-10:00
Industrial IT Security – An essential basis for Industry 4.0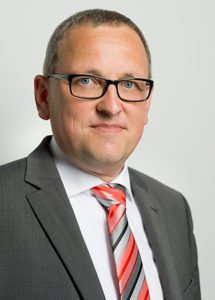
Kai Wollenweber
Program Manager Industrial IT Security
TÜV SÜD Product Service GmbH, Germany
The aspects of information security are gaining an increased public perception, because of factors such as massive denial of service attacks, blackmailing and cyber espionage. Those attacks are by far not limited to the private sector but put also industrial environments and critical infrastructures under risk. Topics like Industry 4.0 and Internet of Things (IoT) are based on dynamic services demanding highly flexible interconnected cyber-physical systems and products. The management and handling of information security is of crucial importance to guarantee the safety and performance of industrial products / systems and is therefore a prerequisite for the acceptance of relevant services and technologies. Security is a risk factor which requires the attention of all involved parties, specifically Product Suppliers/Manufacturers, System Integrators and Asset Owners/Operators in an industrial environment. On the one hand it is a challenging task to specify regulations and standards that can keep up with the highly dynamic requirements. On the other hand new approaches based on common best practices need to be developed in order to address those emerging challenges.
Biography: Kai Wollenweber studied Electrical Engineering at universities in Germany, UK (Aston University), USA (Worcester Polytechnic Institute) and received his M.Sc. from University of Siegen, Germany with focus on data communications. He received his Ph.D. degree in information security in 2002. Before joining TÜV SÜD, one of the world’s leading technical service organizations, in 2013 he worked in various positions in the aerospace & defense and industrial domains, focusing on the topics security & safety. As a Senior Expert and Program Manager Dr. Wollenweber acts as the main contact for all technical inquiries in the area of Industrial IT Security within the organization. In addition he is responsible for the global expansion of related TÜV SÜD services. He is an active member in relevant national and international standardization and conformity assessment committees.
Plenary Talk 5
August 3 (Thursday), 08:30-09:15
Human-Robot Collabrative Cyber Physical System Based Learning of Human Welder Intelligences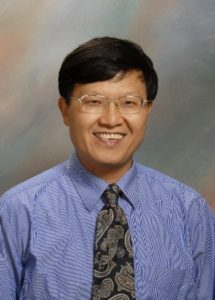
YuMing Zhang
Professor and James Boyd Professor of Electrical Engineering
University of Kentucky, Lexington, Kentucky, USA
A major challenge in learning human welder intelligence arises from the specular nature of pool surface that disqualifies diffuse reflection-based laser triangulation methods. To overcome this issue, the mirror surface is advantageously used to reflect a laser pattern away from the arc, simultaneously eliminating the arc illumination problem. To allow welders to freely demonstrate their skills, a human-robot collaborative system has been established where a welder carries a virtual torch, similarly as operating an actual one, without a sensor. The movement is measured at the virtual system and then followed by a robot which carries the sensor and performs the actual welding. The measured weld pool is displayed to the operator at the virtual site such that the welder can observe the change in the operation result to adjust his/her torch movement and other parameters. The true intelligence of the welder is thus contained in and can thus be extracted from the resultant data. To further extend the ability to unconfined environments, an ultra-compact inertial measurement unit (IMU) has been attached to a manually operated torch to monitor its movement and orientation. To ensure the ultra-high precision needed, a foundation has been established to self adaptively cross calibrate the sensors.
Biography: YuMing Zhang has been with the University of Kentucky, Lexington, Kentucky, USA since 1991. His research in innovative welding processes, sensing and control of welding processes, and intelligent and robotic welding has brought him 180 peer-reviewed journal publications, 8 US patents, and recognitions from The Institution of Mechanical Engineers of the United Kingdom, International Federation of Automatic Control (IFAC), American Welding Society (AWS), and University of Kentucky College of Engineering. Four of his PhD students received the Henry Granjon Prize from the International Institute of Welding (IIW). He currently serves as Lead Principal Reviewer for AWS’ Welding Journal and Associate Editor for IEEE Transactions on Automation Science and Engineering and SME’s Journal of Manufacturing Processes. He has been elected to Fellow of the AWS, ASME, and SME.
Plenary Talk 6
August 3 (Thursday), 09:15-10:00
Intelligent Sensors for Cyber Physical Human Systems
Wen J. Li
Chair Professor of Biomedical Engineering
Dept. of Mechanical and Biomedical Engineering
City University of Hong Kong, Hong Kong
Cyber Physical Human Systems (CPHS) research explores potentially disruptive technologies and novel theories in the integration of sensing, actuation, communication, and computing platforms and algorithms, including robots, sensors, and wireless networks, for advancing human capabilities and improving human lives. CPHS will enable the development of tranformative systems that interact with humans through multiple modalities such as motion, haptic, smell, audio, brain-machine interface, and other new interaction techniques. CPHS will also broaden the advancedment of human capabilities in several realms, including accessing the micro/nano worlds (e.g., single-cell analysis and nano-scale manufacturing), operating in dangerous or inaccessible environments (e.g., monitoring gigantic structures, firefighting, and deep-sea exploration), and improving medical technologies (e.g., rapid drug discovery and ubiquitous healthcare monitoring/delivery). This lecture presents our team’s development of several intelligent sensing platforms based on micro/nano/optical sensors which will enhance diverse CPHS applications spanning from drug discovery to novel interactive technologies and safety monitoring. These platform technologies include human-robot interaction by motion input, mobile human air-bag system, graphene-based motion sensors on wearable flexible substrates, motion recognition for animal drug-testing, robotic palpation sensing fingers for Chinese medicine applications, and optically-induced electrokinetics for single-cell big data analysis.
Biography: Wen J. Li (BSc/MSc, Univ. of Southern California, and PhD, UCLA) is Chair Professor of Biomedical Engineering in the Dept. of Mechanical and Biomedical Engineering of the City University of Hong Kong (CityU). He is currently the President of the IEEE Nanotechnology Council and Director of the Institute for Intelligent Cyber Physical Sensing Syesms of the Shenzhen Academy of Robotics, China. Prior to joining CityU, he was with The Chinese University of Hong Kong (CUHK; 1997-2011), where he headed the Centre for Micro and Nano Systems. He held research positions at the NASA/CalTech Jet Propulsion Laboratory, The Aerospace Corporation, and Silicon Microstructures before moving to Hong Kong in 1997. His team has published more than 300 technical papers related to MEMS/nanotechnology and received best conference/student paper awards from prestigious conferences such as IEEE-ICRA, IEEE/ASME AIM, IEEE-ROBIO, and IEEE-NANO in the past 15 years. Dr. Li served as the Editor-in-Chief of the IEEE Nanotechnology Magazine (2007 to 2013) and is an Editorial Board Member of Scientific Reports. Dr. Li has co-founded 3 startup companies (in Hong Kong and China) which are currently commercializing MEMS and nano-sensor related products worldwide. He was elected IEEE Fellow in 2010 and ASME Fellow in 2011; he is also a Distinguished Overseas Scholar of the Chinese Academy of Sciences. His current research interest includes super-resolution nanoscopy, cyber physical sensors, and micro/nano robotics for biomedical applications.
Keynote Talks
Keynote Talk 1
August 2 (Wednesday), 10:30-11:00
Dynamic Visual Servoing in Uncalibrated Environments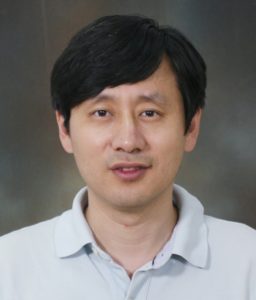
Hesheng Wang
Professor
Department of Automation
Shanghai Jiao Tong University, China
Visual servoing is an important technique that uses visual information for the feedback control of robots. To implement a visual servo controller, an important step is to calibrate the intrinsic and extrinsic parameters of the camera. It is well known that the camera calibration is costly and tedious. The calibration accuracy of these parameters significantly affects the control errors. It is desirable to use uncalibrated visual signals directly in controller design. By directly incorporating visual feedback in the dynamic control loop, it is possible to enhance the system stability and the control performance. Dynamic visual servoing is to design the joint inputs of robot manipulators directly using visual feedback. In the design, the nonlinear dynamics of the robot manipulator is taken into account. In this talk, various visual servoing approaches will be presented to work in uncalibrated environments. These methods are also implemented in many robot systems such as manipulator, mobile robot, soft robot, quadrotor and so on.
Biography: Hesheng Wang received the B.Eng. degree in Electrical Engineering from the Harbin Institute of Technology. Harbin, China, in 2002, the M.Phil. and Ph.D. degrees in Automation & Computer-Aided Engineering from the Chinese University of Hong Kong, Hong Kong, in 2004 and 2007, respectively. From 2007 to 2009, he was a Postdoctoral Fellow and Researcher Assistant in the Department of Mechanical and Automation Engineering, The Chinese University of Hong Kong. He joined Shanghai Jiao Tong University as an Associate Professor in 2009. Currently, he is a Professor of Department of Automation, Shanghai Jiao Tong University, China. He worked as a visiting professor at University of Zurich in Switzerland. His research interests include visual servoing, service robot, robot control and computer vision.
Prof. Wang has published over 100 papers in refereed professional journals and international conference proceedings. He has received a number of best paper awards from major international conferences in robotics and automation. He is an associate editor of Robotics and Biomimetics, Assembly Automation, International Journal of Humanoid Robotics and IEEE Transactions on Robotics. He was a guest editor of Mathematical Problems in Engineering, Journal of Applied Mathematics and International Journal of Advanced Robotic Systems. He served as associate editor in Conference Editorial Board of IEEE Robotics and Automation Society from 2011 to 2015. Prof. Wang is actively involving in organization of international conferences. He served as organizing committee member for many international conferences such as ICRA and IROS. He was the program chair of The 2014 IEEE International Conference on Robotics and Biomimetics, the general chair of The 2016 IEEE International Conference on Real-time Computing and Robotics. He is the program chair of The 2019 IEEE/ASME International Conference on Advanced Intelligent Mechatronics. He was a recipient of Shanghai Rising Star Award in 2014. He is a Senior Member of IEEE.